Biomass pellet presses play a vital role in the production of renewable energy pellets from a variety of organic materials, including wood, agricultural residues, and energy crops. These machines convert raw biomass into high-density pellets through processes involving compression, extrusion, and shaping. To maintain the efficient and reliable operation of a biomass pellet press, it is crucial to regularly inspect and replace key components. This article outlines the primary components that need periodic maintenance and replacement, along with best practices for optimizing the performance and longevity of your biomass pellet press.
1. Pellet Die
The pellet die is one of the most essential components of a biomass pellet press. It shapes raw materials into pellets as they are forced through the die’s holes under high pressure.
Regular Inspection: The die should be routinely inspected for signs of wear, such as enlarged or deformed holes, cracks, or uneven wear patterns. Any damage or significant wear can result in inconsistent pellet quality and reduced production efficiency.
Replacement: The die should be replaced when wear exceeds acceptable limits—typically when hole diameters increase by more than 5% or when the die surface becomes severely pitted or cracked. Using a worn die can lead to poor pellet quality, increased energy consumption, and potential damage to other machine components.
2. Rollers
Rollers work in conjunction with the die to compress biomass material into pellets, applying pressure as the raw material passes through the die.
Regular Inspection: Rollers should be inspected for wear, cracks, or uneven wear patterns. Excessive wear can lead to slippage, reduced pressure, and inconsistent pellet quality.
Replacement: Rollers should be replaced when wear exceeds acceptable limits—typically when the roller surface has worn down by more than 10% of its original thickness or when the surface becomes severely pitted or cracked. Using worn rollers can decrease production efficiency and potentially damage the die and other machine components.
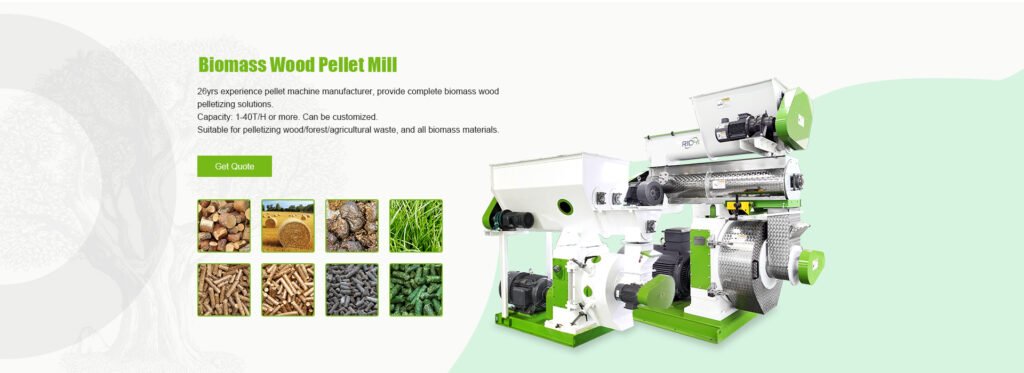
3. Bearings
Bearings support the rotating components of the biomass pellet press, such as the roller shaft and die shaft.
Regular Inspection: Bearings should be checked for signs of wear, including increased vibration, noise, or excessive play in the shaft. Worn bearings can lead to misalignment of the rollers and die, resulting in reduced production efficiency and potential damage to other components.
Replacement: Bearings should be replaced when they show excessive wear or damage, such as pitting, spalling, or excessive clearance in the shaft. Using worn bearings can lead to premature failure of other components and potential downtime.
4. Gearbox
The gearbox transmits power from the motor to the roller and die shafts, ensuring the appropriate speed and torque are applied to the biomass material during the pelleting process.
Regular Inspection: The gearbox should be inspected for signs of wear, such as increased noise, vibration, or lubricant leakage. Worn gears or bearings can reduce efficiency and potentially damage other components.
Replacement: The gearbox should be replaced when it shows signs of excessive wear or damage, such as pitting or chipping of the gear teeth or excessive bearing wear. Using a worn gearbox can lead to reduced production efficiency and potential downtime.
5. Lubrication System
The lubrication system provides adequate lubrication to various moving components of the biomass pellet press, including bearings, gears, and chains.
Regular Inspection: The lubrication system should be regularly inspected for signs of leakage, contamination, or insufficient lubrication. Inadequate lubrication can lead to excessive wear and potential damage to machine components.
Replacement: Lubricants should be replaced at intervals specified by the manufacturer to ensure they maintain their lubricating properties and do not become contaminated with wear particles or other foreign matter. Using contaminated or degraded lubricant can lead to excessive wear and potential damage.
6. Maintenance Practices
Regular maintenance is essential for ensuring optimal performance and longevity of a biomass pellet press. Best practices include:
- Establishing a Maintenance Schedule: Implement a schedule for daily inspections, weekly lubrication, and periodic replacement of wear parts.
- Following Manufacturer Recommendations: Always refer to the machine manual for specific maintenance procedures and replacement intervals.
- Using Quality Replacement Parts: Invest in genuine or approved replacement parts to ensure the machine operates at peak efficiency and minimizes the risk of premature wear or failure.
- Keeping the Machine Clean: Regularly clean the machine and its components to prevent the buildup of dust, debris, and foreign materials that can contribute to wear and damage. (Related post: straw pelletizer)
Conclusion
Regular inspection and replacement of key components are essential for maintaining the optimal performance and lifespan of a biomass pellet press. By focusing on the die, rollers, bearings, gearbox, and lubrication system while adhering to best maintenance practices, you can ensure your machine operates efficiently, produces high-quality pellets, and minimizes downtime due to unexpected failures.
Investing in regular maintenance and replacement of wear parts may require upfront costs but can yield significant long-term benefits by reducing operating costs, improving product quality, and extending the useful life of your biomass pellet press. As the demand for renewable energy sources continues to rise, ensuring the reliability and efficiency of your biomass pellet production equipment will be crucial for success in this dynamic and rapidly evolving industry.