Classification of Animal Feed Production Plants by Animal
Animal feed production plant is specialized facilities designed to manufacture feed tailored to the nutritional needs of different animal species. These plants are classified based on the type of animals they serve, with each category focusing on specific dietary requirements and formulations. This classification ensures that every animal receives optimal nutrition, promoting health, productivity, and overall well-being.
Poultry feed production plants cater to the dietary needs of chickens, turkeys, ducks, and other birds. These plants produce feed that is rich in proteins, vitamins, and minerals essential for the growth, egg production, and overall health of poultry. The formulations often include grains, soybean meal, and various additives that enhance the feed’s nutritional value.
Cattle feed production plants target the nutritional demands of dairy and beef cattle. These plants produce balanced feeds that provide adequate energy, protein, fiber, and minerals necessary for milk production, growth, and weight gain. The feeds often include corn, silage, alfalfa, and supplementary minerals to support the cattle’s digestive system and overall health.
Swine feed production plants focus on the dietary needs of pigs, from piglets to mature swine. The feed produced here is formulated to ensure proper growth, reproduction, and meat quality. High-energy grains, soybean meal, and essential amino acids are typically included to meet the swine’s nutritional requirements and to promote efficient feed conversion.
Fish feed production plants cater to various species of farmed fish, such as tilapia, salmon, and catfish. The feed produced in these plants is designed to float or sink, depending on the feeding habits of the fish species. The formulations are rich in proteins, fats, vitamins, and minerals, supporting rapid growth, disease resistance, and high-quality flesh production.
Pet feed production plants manufacture food for companion animals like dogs and cats. These plants create diets that cater to pets’ unique nutritional needs, focusing on balanced levels of proteins, fats, carbohydrates, vitamins, and minerals. The ingredients often include meat, grains, vegetables, and specialized supplements to maintain pets’ health and vitality.
Each category within an animal feed production plant is tailored to meet the specific nutritional demands of the respective animals. This targeted approach ensures that every feed produced not only sustains the animal but also enhances its growth, productivity, and overall health.
Essential Equipment in Animal Feed Production Plants
Animal feed production plants rely on a range of specialized machinery to convert raw ingredients into nutritionally balanced feed for livestock. Each piece of equipment plays a distinctive role, ensuring the feed produced meets quality and safety standards. Understanding these functions is crucial for effectively managing an animal feed production plant.
Mixers are among the fundamental components, responsible for blending different ingredients into a homogeneous mixture. Proper mixing ensures that every pellet or flake of feed contains a balanced proportion of nutrients, essential for animal health and growth. These mixers may range from small batch mixers to large industrial-scale continuous mixers, catering to different production scales.
Grinders, also known as hammer mills or roller mills, are used to reduce the size of raw ingredients. By breaking down materials into smaller particles, grinders enhance the digestibility of the feed. This step is particularly important for grains and other hard components. Efficient grinding not only improves nutrient absorption but also facilitates subsequent processing stages.
Pellet mills are a critical part of animal feed production plants, transforming the mixed ingredients into firm, homogeneous pellets. Pelleting compacts the feed, making it easier to handle and store, while also improving feed efficiency by minimizing waste. The pellet mill operates by pressing the powdered feed through a die, forming uniform pellets that maintain their shape.
Extruders serve a specialized function, particularly for producing high-quality feed for fish and pets. By cooking the ingredients under high pressure and temperature, extruders produce feed with enhanced digestibility and palatability. This process also allows for the incorporation of various additives, further enriching the feed’s nutritional profile.
Cooling systems are indispensable in the final stages of feed production. After pelleting and extrusion, the feed is often hot and moist, requiring cooling to preserve its quality and prevent spoilage. Cooling systems rapidly reduce feed temperature and moisture content, ensuring the final product is stable and long-lasting.
In essence, each type of equipment in an animal feed production plant works synergistically to ensure the production of high-quality, nutrient-rich animal feed. By understanding and maintaining these machines, operators can optimize their production processes, achieving both efficiency and product excellence.
Sections of an Animal Feed Pellet Factory
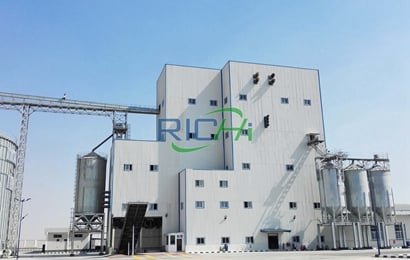
An animal feed production plant is composed of several key sections, each serving a pivotal role in the systematic production of high-quality pellet feed. The first crucial area is the ingredient storage section. This section is designated for storing raw materials such as grains, proteins, vitamins, and minerals. Containers and silos are often utilized to maintain the quality and safety of these ingredients, ensuring they are protected from external contaminants.
Next, materials move to the grinding section. Here, raw ingredients are ground into smaller particles to maximize surface area, thus enhancing the efficiency of subsequent processes. Advanced grinding equipment, including hammer mills and roller mills, are used to ensure a uniform particle size, which is integral for the consistent quality of the pellets.
Following grinding, the materials proceed to the batching and mixing section. Accurate batching systems ensure precise measurement and combination of various ingredients according to specific formulations. The mixture is then homogenized using high-speed mixers to guarantee uniform distribution of nutrients and ingredients throughout the feed.
The homogenized mixture is then transported to the pelleting section. This is where the raw feed is fed into pellet mills, undergoing the process of compaction and extrusion to form pellets. The temperature and moisture control in this section are meticulously regulated to attain optimal pellet density and nutritional value.
Once formed, the feed pellets enter the cooling and screening section. Cooling systems reduce the temperature of the hot, freshly formed pellets to prevent spoilage and preserve nutritional quality. Screening machines further ensure that only pellets of desired size are passed forward, removing any irregular or fine particles.
Finally, the finished product reaches the packaging section. This section involves the packaging of pellets into bags or bulk containers for ease of transportation and storage. Automated packaging systems enhance efficiency, maintaining the physical integrity and nutritional composition of the feed while preparing it for distribution.
Effectively, each section within an animal feed production plant is interconnected, playing a vital role in maintaining the quality and efficiency of the production process. From storage to final packaging, the systematic flow of materials ensures that high standards are upheld, ultimately delivering quality feed to end-users.
Introduction and Production Capabilities of Richi Animal Feed Production Plant
Richi’s animal feed production plant stands as a beacon of innovation and efficiency in the feed industry. Emphasizing advanced production capabilities, this state-of-the-art facility incorporates cutting-edge technologies and sophisticated machinery that ensure the production of high-quality animal feed. Richi harnesses precision engineering and automated systems, minimizing human error and optimizing throughput. The plant’s ability to produce a wide variety of feeds—from poultry to livestock and aquatic species—demonstrates its versatility and commitment to serving diverse market needs.
One of the unique strengths of the Richi animal feed production plant lies in its robust quality control measures. Each production stage is meticulously monitored, ensuring that every batch of feed meets stringent safety and nutritional standards. Adopting a comprehensive approach to quality assurance, the plant employs advanced testing laboratories and highly trained personnel specializing in feed analysis and formulation. This meticulous attention to detail guarantees that animal feed from Richi not only promotes animal health but also complies with international regulatory requirements.
Furthermore, the plant’s scalability addresses both small and large-scale production needs, making it adaptable to various market demands. Its design allows for rapid adjustments in production volumes without compromising quality. This flexibility is pivotal for meeting seasonal demand fluctuations and accommodating the specific requirements of different animal husbandry practices.
Efficiency is another cornerstone of the Richi animal feed production plant. The integration of energy-saving technologies and optimized production processes result in decreased operational costs and a reduced environmental footprint. Richi’s commitment to sustainability is evident through its initiatives to recycle production waste and reduce emissions, positioning the plant as an eco-friendly leader in the industry. By constantly refining its operational capabilities, Richi ensures that it remains at the forefront of the animal feed production sector, delivering superior products with unparalleled consistency.
Global Reach: Countries Where Richi Animal Feed Production Plant Has Been Sold
Richi animal feed production plant has established a significant global footprint, demonstrating their capability and reliability across diverse markets. Today, these state-of-the-art production facilities are operational in various countries across multiple continents, including North America, Europe, Asia, and Africa. This widespread presence underscores the international appeal and trust that Richi has cultivated over the years within the animal feed production industry.
In North America, Richi’s plants have bolstered the feed production capacities in countries such as the United States and Canada. By integrating advanced technologies, these installations have significantly improved the efficiency and quality of feed production, catering to the region’s high standards and robust demand. Success stories from leading agribusiness firms in these countries highlight the substantial gains in operational efficiencies and product quality, ensuring that livestock receive the best possible nutrition.
Europe is another critical market for Richi’s animal feed production plants, with notable installations in Germany, France, and the United Kingdom. These countries have stringent regulatory requirements, and Richi’s facilities have consistently met and exceeded these standards. Testimonials from European clients frequently emphasize the reliability, precision, and scalability of Richi’s machinery, enabling them to achieve higher throughput while maintaining rigorous quality controls.
Asia, with its rapidly expanding agricultural sector, has also benefitted from Richi’s innovative solutions. Countries like China, India, and Vietnam have seen a significant improvement in animal feed production capacities due to Richi’s state-of-the-art plants. Local farmers and feed manufacturers praise the company’s commitment to innovation and support, citing increased productivity and reduced operational costs as major advantages.
In Africa, where sustainable and efficient agriculture is crucial, Richi’s feed production plants have made a substantial impact. Nations such as Nigeria, South Africa, and Kenya now host these advanced systems, which have helped mitigate feed shortages and enhance animal health and welfare. Success stories from these regions often highlight the transformational impact of Richi’s technology on local farming communities, contributing to improved food security and economic growth.
Feed pellet factories are integral to the animal feed production plant industry, operating globally with notable regional variations in practices, challenges, and trends. In North America, for instance, the focus often lies on maximizing efficiency and leveraging advanced technologies to streamline production processes. This region is characterized by large-scale factories that benefit from economies of scale, significantly contributing to the high output and consistency in quality. One prominent example is a major facility in the United States that employs state-of-the-art automation and data analytics to ensure optimal feed formulation and production efficiency.
Conversely, in developing regions such as parts of Africa and Asia, feed pellet factories often face unique challenges. Issues such as access to quality raw materials, infrastructural deficits, and financial constraints can impede production capacities. Yet, these regions are also witnessing innovative approaches to overcome these hurdles. In India, for example, small-scale feed pellet businesses are thriving due to adaptable technology and community-based feed production models, thereby supporting local agriculture and livestock sectors.
European feed pellet factories are notable for their stringent adherence to regulatory standards and environmental sustainability objectives. The European Union mandates comprehensive safety protocols and quality control measures in animal feed production, influencing factories to adopt sustainable practices. A noteworthy case study is a leading factory in Germany that focuses on producing organic feed pellets, using renewable energy sources and engaging in circular economy practices.
Trends in the global animal feed industry indicate an increasing preference for specialized feeds, driven by escalating demand for quality animal produce. This shift is evident in places like Australia, where feed pellet factories are emphasizing high-nutrient formulations tailored to specific livestock requirements. Additionally, technological innovations such as IoT-enabled smart factories and AI-driven quality assurance systems are gaining traction, paving the way for more sophisticated and efficient animal feed production plants.
Ultimately, feed pellet factories across different regions are adapting to their respective environmental, economic, and regulatory contexts, contributing significantly to the global agriculture landscape. Their evolution continues to be shaped by ongoing advancements and the changing demands of agricultural practices worldwide.
Steps to Building an Animal Feed Production Plant
Establishing an animal feed production plant requires thorough planning and execution. The initial stage involves meticulous planning, where you outline your business objectives, determine market demand, and develop a comprehensive business plan. Next, securing funding becomes pivotal; explore various financing options such as bank loans, investors, and government grants tailored for agricultural enterprises.
Site selection is another critical step in the process. When choosing a location, consider factors such as proximity to raw material suppliers, transportation facilities, and access to utilities. The site should be strategically placed to minimize logistics costs and maximize operational efficiency. Zoning laws and environmental regulations must also be carefully reviewed to ensure compliance.
Once the site is selected, acquiring the necessary equipment is essential. The equipment must be suitable for the scale of your animal feed production plant and compatible with the feed types you intend to produce. This encompasses grinders, mixers, pellet mills, and packaging machines. Consulting with industry experts can provide valuable insights into selecting the right machinery.
Obtaining the required permits and licenses is another fundamental aspect. This includes business registration, environmental clearances, and health and safety certifications. Regulatory compliance ensures the plant operates within legal frameworks and adheres to industry standards.
Designing an efficient production line is paramount for maximizing productivity and minimizing waste. The layout should facilitate smooth workflow, from raw material intake to final product packaging. Consideration of automation technologies can further enhance operational efficiency and product consistency.
Finally, the training of personnel is imperative. Employees must be well-trained in operating machinery, adhering to safety protocols, and maintaining quality control standards. Ongoing training programs and regular updates on industry advancements help in sustaining high performance and safety levels.
In essence, constructing an animal feed production plant involves a comprehensive approach, ensuring each phase is meticulously planned and executed to achieve a seamless, efficient, and compliant operation.
Cost of Setting Up an Animal Feed Production Plant
Setting up an animal feed production plant entails a significant financial commitment, but thorough planning and understanding of the costs involved can ensure the investment leads to profitable returns. The initial investment is primarily directed towards the purchase of machinery and equipment. This includes grinders, mixers, pellet mills, cooling and packaging machines, and other essential components that comprise a functional animal feed production line. Depending on the scale of the operation and technology selection, machinery costs can range from $50,000 to several hundred thousand dollars.
In addition to the cost of equipment, installation expenses form a substantial part of the initial outlay. These cover the construction of the plant facility, installation of machinery, and setting up necessary utilities such as water, electricity, and air conditioning systems. Operational expenses encompass raw material procurement, labor, energy consumption, and utility costs. Feeding plants require a steady supply of raw ingredients like grains, protein sources, and additives, which represent a recurring financial burden.
Maintenance is another critical financial consideration, as regular upkeep and part replacement are essential to maintaining optimal performance and prolonging the lifespan of the machinery. Annual maintenance can account for 5-10% of the total equipment cost, depending on usage intensity and environmental factors.
Pursuing various funding options can alleviate some of the financial pressure. These may include business loans, government grants, and investment from stakeholders. Tailored financial packages from banks and financial institutions can finance the initial costs, with repayment schedules aligned with the business’s cash flow cycles. Venture capital and private equity are viable alternatives if a scalable and innovative business model is proposed.
The anticipated return on investment (ROI) in an animal feed production plant depends on factors such as market demand, production efficiency, and cost management. Typically, a well-operated plant can recoup the initial costs within 2-5 years, contingent upon effective marketing and sales strategies. Conducting comprehensive market research and financial analysis is vital to ensure the venture’s sustainability and profitability.