The Significance of Building a Wood Pellet Factory
The establishment of a wood pellet factory holds significant economic and environmental advantages in today’s landscape of renewable energy. As global efforts intensify to reduce dependency on fossil fuels, the demand for sustainable energy sources has surged. Wood pellets, owing to their efficiency and lower carbon emissions, have become a preferred biomass fuel option among these green energy solutions. Building a wood pellet factory not only addresses this escalating demand but also contributes to the broader objective of decreasing global carbon footprints.
Transitioning to wood pellets as a fuel source helps mitigate climate change by ensuring a reduction in both greenhouse gases and particulate matter when compared to traditional coal or oil. This is pivotal in assisting nations to meet their environmental targets and agreements. Moreover, the carbon neutrality of wood pellets, derived from sustainably managed forests, ensures continuity in carbon cycles, balancing carbon release and absorption effectively.
Economically, wood pellet factories create numerous job opportunities, stimulating local economies and providing stable employment in rural areas. From forest management, which involves the sustainable harvesting of wood and maintaining forest health, to the factory operations and transportation logistics, the demand for skilled labor spans a wide range of sectors. These factories thus serve as pivotal nodes in rural development, generating secondary businesses and supporting infrastructure improvements.
Additionally, wood pellet factories foster sustainable forest management practices. By optimizing the use of wood residues and low-grade wood that would otherwise go to waste, these factories encourage the efficient utilization of forest resources. This not only enhances forest health but also supports biodiversity, as forests are less likely to be clear-cut when managed sustainably.
The socio-economic benefits coupled with environmental sustainability firmly position wood pellet factories as integral players in the transition towards a greener, more sustainable future.
Advantages of Wood Pellets
Wood pellets offer a myriad of advantages as a fuel source, making them a compelling choice for both residential and industrial applications. One of the primary benefits is their high energy efficiency. Compared to traditional fossil fuels, wood pellets have a lower moisture content, which results in higher combustion efficiency. This characteristic ensures that more energy is harnessed from each unit of fuel, making wood pellets a highly efficient energy source.
Another crucial advantage is their lower carbon emissions. When burned, wood pellets release significantly less carbon dioxide compared to fossil fuels such as coal, oil, and natural gas. This reduction in carbon emissions contributes positively to the global effort in combating climate change, making wood pellets a more sustainable and environmentally friendly option.
Cost-effectiveness is another critical factor in favor of wood pellets. The manufacturing processes in a wood pellet factory are often optimized to make wood pellets more affordable than many fossil fuels. Moreover, the price stability of wood pellets, in contrast to the often volatile prices of fossil fuels, provides an economic advantage, particularly for large-scale consumers.
Ease of handling and storage adds to the practicality of using wood pellets. These pellets are compact and standardized in size, which simplifies the logistics of transportation, storage, and refueling. Specially designed storage systems ensure that wood pellets remain dry and in optimal condition, minimizing waste and ensuring consistent energy output.
Lastly, wood pellets contribute to energy security by reducing reliance on imported fuels. Utilizing locally sourced wood and residual biomass for pellet production not only supports local economies but also reduces vulnerabilities associated with energy imports. This shift towards self-sufficient energy generation further underscores the strategic importance of investing in a wood pellet factory.
How to Choose a Wood Pellet Extruder Machine
When embarking on the journey of establishing a wood pellet factory, selecting the appropriate wood pellet extruder machine is paramount. The right machine can significantly influence the efficiency and output of your production line. Several factors demand careful consideration to ensure optimal machine performance.
Firstly, production capacity is a crucial determinant. Depending on your factory’s anticipated production volume, you must select a model that aligns with these needs. Machines vary in their throughput rates, and choosing one that suits your scale of operation will prevent bottlenecks and underutilization.
Energy efficiency is another vital aspect. In the context of rising energy costs and environmental concerns, machines that minimize energy consumption can lead to substantial savings over time. Assess the energy ratings of various models to identify those that offer superior energy efficiency without compromising on output quality.
Ease of maintenance is a factor that cannot be overlooked. Machines with complex maintenance requirements could lead to prolonged downtime and increased operational costs. Opt for designs that facilitate straightforward maintenance procedures, potentially with features like accessible parts and automated cleaning mechanisms.
Cost is an inevitable consideration. However, rather than opting for the cheapest option, it is imperative to evaluate the machine’s cost relative to its features and expected lifespan. A higher initial investment in a durable and efficient extruder can prove more economical in the long run.
Technological features should also be on your radar. Modern wood pellet extruder machines come equipped with advanced control systems, automatic feed mechanisms, and other innovations that enhance operational accuracy and reliability. Prioritize machines with features that align with your factory’s specific needs.
Durability ties into the machine’s lifespan and its ability to withstand rigorous use. Machines constructed from robust materials with a reputation for long-term durability are preferable. Additionally, the manufacturer’s reputation in the industry is indicative of the machine’s reliability and the support you can expect post-purchase. Engaging with reputable manufacturers who offer comprehensive warranties and excellent customer service is beneficial.
Richi Wood Pellet Extruder Machine for Sale
Richi wood pellet extruder machine is well-regarded in the industry for their advanced features and top-notch performance. Known for their robustness and efficiency, these machines cater to varying production needs, from small-scale operations to large commercial wood pellet factories. At the core of Richi’s offerings are high-quality engineering and a commitment to customer satisfaction.
One of the defining features of Richi’s wood pellet extruder machines is their technical specifications. These machines come with high torque, precision gear transmission systems, and a customizable pelletizing chamber, ensuring consistent pellet quality and high output rates. The energy-efficient motors combined with advanced control systems provide users with the ability to optimize production processes, thereby reducing operational costs.
Richi’s wood pellet extruder machines also offer extensive customization options to meet specific production requirements. Users can select from a variety of die sizes, automated feeding systems, and conditioning techniques to achieve the desired pellet characteristics. This flexibility is critical for adapting to different types of raw materials, such as hardwood, softwood, and agricultural residues.
After-sales service is another cornerstone of Richi’s customer-centric approach. The company provides comprehensive support, including installation, training, and ongoing technical assistance. This ensures that customers can fully leverage the capabilities of their wood pellet extruder machines. Additionally, Richi offers regular maintenance services and quick access to genuine spare parts, enhancing the longevity and reliability of their equipment.
Customer feedback highlights the reliability and efficiency of Richi’s wood pellet extruder machines. Many users appreciate the ease of operation and the significant reduction in downtime due to the machine’s durability. The favorable reviews reflect Richi’s commitment to high-quality products and excellent customer service, setting them apart from competitors in the industry.
Overall, Richi’s wood pellet extruder machines represent a compelling choice for anyone aiming to establish or upgrade a wood pellet factory. Their cutting-edge features, customizable options, and strong after-sales support make them a valuable asset in the wood pellet production landscape.
Advantages of Richi Biomass Wood Pellet Machines
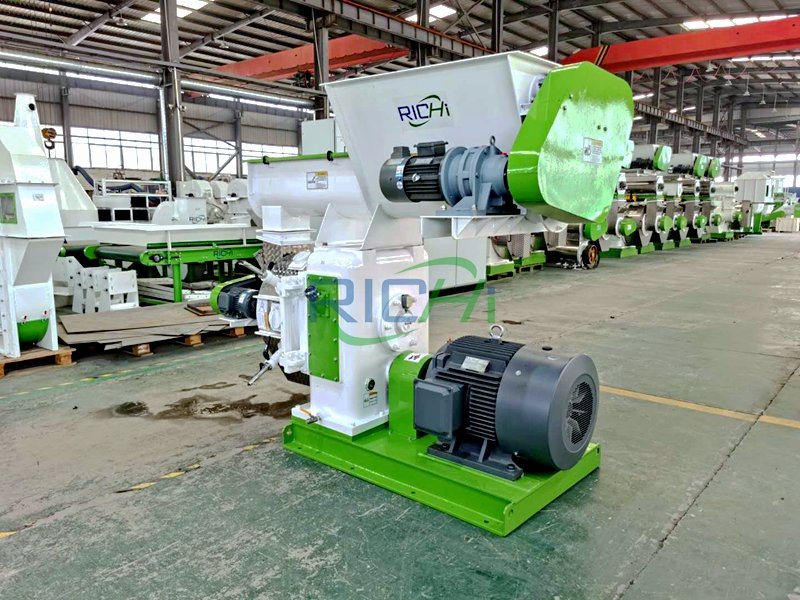
Richi biomass wood pellet machine stands out in the market due to their advanced technology, which ensures efficient and precise pellet production. The integration of state-of-the-art technology facilitates optimal performance and maximizes production output, making these machines a preferred choice for many industries. This technological edge not only enhances productivity but also ensures the consistent quality of wood pellets, thereby meeting stringent industry standards.
Energy efficiency is another significant advantage offered by Richi biomass wood pellet machines. These machines are designed to minimize energy consumption while maximizing output, which translates to reduced operational costs and a lower carbon footprint. The energy-efficient nature of these machines aligns with the growing emphasis on sustainable industrial practices and supports the move towards greener manufacturing solutions.
Robustness and durability are core attributes of Richi pellet machines. Constructed with high-quality materials, these machines ensure longevity and withstand the rigors of continuous use. The durable design also means fewer breakdowns and less maintenance, contributing to a smooth and cost-effective operation. This reliability is particularly beneficial for wood pellet factories aiming for uninterrupted production and minimal downtime.
User-friendly design is a hallmark of Richi biomass wood pellet machines. These machines are engineered for ease of use, featuring intuitive controls and easy-to-understand interfaces. This user-centered approach not only enhances operational efficiency but also reduces the learning curve for new operators, ensuring that factories can quickly adapt and optimize their pellet production processes.
Additionally, Richi offers comprehensive after-sales support, ensuring that customers receive ongoing assistance and maintenance services. This support system is crucial in addressing any operational challenges and maintaining the optimal performance of the machines. The availability of spare parts and expert technical assistance further bolsters the reliability of Richi’s machinery in the long term.
The sustainability and environmental benefits of using Richi pellet machines are noteworthy. By converting biomass into high-quality pellets, these machines support waste reduction and energy recovery, promoting a circular economy. The lower emissions during pellet production also contribute to a cleaner environment, making Richi biomass wood pellet machines an eco-friendly choice for industrial operations.
Relationship Between the Price of Wood Pellet Machines and Their Features
The price of wood pellet machines is influenced by an array of features and specifications that determine their overall functionality and efficiency. One primary factor affecting the cost is the production capacity of the machine. Machines with higher output capacities are generally more expensive due to their advanced technology and higher operational efficiency. These machines are capable of producing larger quantities of wood pellets in shorter time frames, thus justifying their higher price tags.
Another critical factor is the level of automation integrated into the wood pellet factory machinery. Fully automated machines, which require minimal human intervention and offer enhanced precision and consistency, command a premium compared to semi-automated or manual variants. Automation not only improves productivity but also reduces the potential for human error, contributing to the higher cost.
The materials used in manufacturing significantly impact the price as well. Machines constructed with high-quality, durable materials such as stainless steel or heavy-duty alloys are more expensive than those made from standard materials. These premium materials ensure longevity and resistance to wear and tear, making them a worthwhile investment for large-scale operations.
Brand reputation also plays an essential role in the pricing of wood pellet machines. Established brands with a proven track record of reliability and customer satisfaction tend to price their machines higher. This is often due to superior research and development, stringent quality control measures, and comprehensive after-sales support.
When seeking to balance cost and quality, it is crucial for prospective buyers to evaluate their specific needs and operational goals. Investing in a higher-priced, high-capacity, fully automated machine may be more cost-effective in the long run for a large-scale wood pellet factory. Conversely, smaller operations might find that a mid-range machine with standard features and reliable brand reputation provides an ideal balance between performance and affordability.
The Production Process of Wood Pellets
The efficient operation of a wood pellet factory hinges on understanding the intricate steps involved in the production process. It begins with raw material preparation, typically involving the collection and selection of suitable wood sources such as sawdust, wood chips, or logs. Proper selection of raw materials is crucial as it directly influences the final product quality. Once selected, the raw materials undergo size reduction to ensure a uniform particle size conducive to pelletizing; this step often involves chipping and grinding to achieve the desired consistency.
Following material preparation, the next critical stage is drying. The moisture content of wood must be reduced to around 10-15%, an optimal range that facilitates energy-efficient pelletizing and ensures product quality. Drying typically employs drum dryers or rotary dryers, technologies that offer consistent and controllable methods to achieve the necessary moisture reduction.
Once adequately dried, the materials proceed to grinding. This process further ensures the uniformity of particle sizes, which is essential for producing high-quality wood pellets. Hammer mills or other specialized grinding equipment reduce the wood into fine particles, preparing them for the subsequent pelletizing process.
Pelletizing is the core step in producing wood pellets. Using pellet mills, the finely-ground materials are compressed through die holes under high pressure and temperature, forming dense, cylindrical pellets. This stage not only gives the pellets their form but also enhances their durability and calorific value. Operators must carefully monitor parameters such as pressure, temperature, and feed rate to optimize pellet quality and manufacturing efficiency.
After pelletizing, the hot pellets must be cooled before packaging. Cooling helps stabilize the pellets’ structure and reduces the risk of mold or decay. Counterflow coolers are commonly used, which cool the pellets efficiently and uniformly. Following the cooling process, the wood pellets are ready for packaging, which involves weighing, bagging, and sealing the pellets in moisture-proof bags to maintain their quality during storage and transportation.
Optimizing each step of the production line— from raw material preparation through to packaging— is essential for maximizing efficiency in a wood pellet factory. Continuous monitoring and fine-tuning of the process parameters help in producing high-quality wood pellets while minimizing waste and energy consumption.
Raw Materials for Wood Pellets
Building and operating a wood pellet factory necessitates a comprehensive understanding of the raw materials utilized in the production process. Among the most common sources are hardwood, softwood, sawdust, wood chips, and agricultural residues. Each material offers distinct characteristics that influence the quality, efficiency, and cost-effectiveness of wood pellet production.
Hardwood, sourced from trees such as oak, maple, and birch, is highly prized for its dense and durable pellets. The high calorific value and prolonged burning time make hardwood pellets an excellent choice for heating applications. However, hardwood is often more expensive and less readily available due to slower growth rates and higher demand in other industries. Its suitability for pellet machines is dependent on advanced equipment capable of handling denser materials.
Softwoods like pine, spruce, and fir are more abundant and grow faster, resulting in a more economical option for wood pellet factories. Softwood pellets tend to have a higher resin and natural oil content, which can enhance the combustion process, though they might produce more ash. Their softer, fibrous structure generally facilitates easier processing in standard pellet machines, allowing for widespread use in various heating systems.
Sawdust, a byproduct of the lumber and woodworking industries, is another valuable material for wood pellet production. Utilizing sawdust helps minimize waste and lowers raw material costs. Although sawdust’s light, fine consistency allows for easier pelletization, it might necessitate additional drying and binding agents to achieve optimal pellet quality. This byproduct’s availability can vary based on the surrounding industrial activity.
Wood chips, sourced from logging, milling, and other wood processing operations, offer a robust alternative for pellet manufacturing. This material is available in a range of sizes, which necessitates pre-processing to ensure uniformity before pelletizing. Wood chips combine the benefits of cost-efficiency and substantial output volume, making them a popular choice for large-scale operations.
Lastly, agricultural residues, such as straw, corn stalks, and husks, provide an intriguing option. These byproducts of farming activities are abundant and typically lower in cost. Nevertheless, they may require specialized pellet machines due to lower lignin content, and might need to be blended with wood materials for enhanced pellet quality and machine compatibility.
In essence, a wood pellet factory must carefully evaluate the types of raw materials available, considering factors like cost, availability, and machine suitability. This ensures the production of high-quality pellets while optimizing operational efficiency and resource utilization.
Countries Leading in Wood Pellet Production and Factories
In the realm of sustainable energy solutions, several countries stand out for their significant contributions to the wood pellet industry. These nations have honed their resources and policies to lead in wood pellet production, making notable impacts on global markets. Among the prominent players are the USA, Canada, Sweden, Germany, and Russia, each leveraging unique advantages to maintain leading positions in this sector.
The United States is a major force in the wood pellet market. Abundant forestry resources and a well-developed infrastructure support substantial production volumes. Additionally, policies promoting renewable energy and sustainability have spurred growth in the wood pellet industry. The USA benefits from advanced technology and large-scale facilities that ensure efficient and high-quality production.
Similarly, Canada’s vast forest reserves provide an ample supply of raw materials essential for wood pellet production. The country’s robust forestry management practices ensure sustainability, effectively balancing environmental concerns with industrial growth. Canadian governmental policies encourage the development of renewable energy sources, further boosting the wood pellet sector.
In Europe, Sweden and Germany are leaders in wood pellet manufacturing. Sweden’s commitment to reducing carbon emissions and its plentiful supply of softwood make it a key player in the industry. With strong government incentives and a rigorous focus on renewable energy, Sweden consistently produces high quantities of wood pellets for domestic use and export.
Germany’s success in wood pellet production can be attributed to its advanced technology and favorable government policies supporting renewable energy. The country’s efficient utilization of wood processing by-products ensures a steady supply of raw materials for pellet production. Germany’s wood pellet factories benefit from innovations that enhance productivity and environmental sustainability.
Russia’s substantial forested areas position it as another crucial player in this market. The country boasts one of the largest wood reserves globally, providing a solid foundation for wood pellet production. Russian government policies increasingly focus on optimizing forest resource utilization and promoting renewable energy, fostering growth in wood pellet output.
The convergence of raw material availability, cutting-edge technology, and supportive governmental policies in these nations underscores their leadership in the wood pellet industry. Their contributions are pivotal in advancing global energy sustainability and reducing reliance on fossil fuels.
Installing and commissioning Richi wood pellet machinery is a pivotal phase in the establishment of a wood pellet factory. The process embarks with meticulous pre-installation preparations that include site selection and layout planning. Ensuring adequate space and optimal workflow are crucial for efficient operations. The designated site should support stable power supply and appropriate ventilation, necessary for the proper functioning of the machinery.
Subsequently, the assembly stage involves the systematic integration of various components of the wood pellet machinery. Skilled technicians, thoroughly acquainted with Richi equipment, should handle this task to guarantee that all parts are correctly and securely positioned. Detailed assembly instructions provided by Richi must be meticulously followed to mitigate any risk of malfunction or suboptimal performance.
Post-assembly, the machinery undergoes a rigorous testing phase. This involves running the wood pellet machinery under operational conditions to ensure it performs as expected. During this stage, parameters like temperature, moisture content, and pellet density are closely monitored. Any discrepancies from the standard operational benchmarks necessitate immediate adjustments and fine-tuning.
An integral aspect of commissioning is troubleshooting potential issues that may arise during the initial runs. Richi provides extensive documentation and detailed guidelines to aid in diagnosing and resolving common challenges. Ensuring that the equipment functions without hitches involves meticulous inspection of each component and process undertaken by the wood pellet factory.
Richi’s support extends beyond the initial installation and commissioning. They offer comprehensive training programs designed to equip operators with the necessary skills to manage and maintain the wood pellet machinery effectively. These training sessions encompass best practices, safety protocols, and efficient handling techniques, ensuring the operators are well-prepared to handle daily operations and unforeseen issues efficiently.
In addition, Richi’s customer support is readily available for any assistance required, facilitating smooth and efficient commissioning of the machinery. Their support services ensure that the wood pellet factory can operate at optimal capacity, contributing to its long-term success and productivity.