In the realm of modern agriculture and animal husbandry, the utilization of alfalfa pellets has gained significant traction owing to their versatility and nutritional benefits. Central to the production of these pellets is the alfalfa pellet making machine, a sophisticated piece of equipment designed to streamline the conversion process of raw alfalfa material into high-quality pellets.
In this article, we delve into the intricacies of alfalfa pellet making machines, exploring their uses, market analysis, operational principles, project cases, supplier selection, and the indispensable role of RICHI Machinery in this domain.
Understanding Alfalfa Pellet Making Machines
Alfalfa pellet making machines are specialized equipment tailored for the processing of alfalfa, a perennial flowering plant widely cultivated for animal feed due to its high protein content and digestibility.
These machines facilitate the compression of finely ground alfalfa material into compact pellets, enhancing its storage, transportation, and utilization efficiency. The resulting pellets serve as a convenient and nutritious feed option for livestock, including cattle, horses, sheep, and rabbits, among others.
Market Analysis and Profit Point Analysis
The demand for alfalfa pellets continues to surge, driven by the growing awareness of their nutritional benefits and the increasing emphasis on efficient animal feed management practices. Market analysis reveals a robust growth trajectory for alfalfa pellet production, with a notable surge in demand from livestock farmers, feed mills, and animal husbandry enterprises.
Profit point analysis indicates promising returns on investment in alfalfa pellet making machines, with significant opportunities for revenue generation through the sale of pellets in domestic and international markets.
Operational Principles and Application
Alfalfa pellet making machines operate on the principle of compressing finely ground alfalfa material through a die to form cylindrical pellets of uniform size and density.
The process involves several stages, including raw material preparation, grinding, conditioning, pelletizing, cooling, and packaging. These machines are versatile, capable of processing various types of alfalfa feedstock, including fresh alfalfa, dried alfalfa, and alfalfa meal, to produce pellets tailored to specific nutritional requirements and animal feeding preferences.
The resulting pellets find extensive application in livestock farming, dairy production, poultry farming, and pet food manufacturing, offering a convenient and cost-effective solution for meeting the dietary needs of animals.
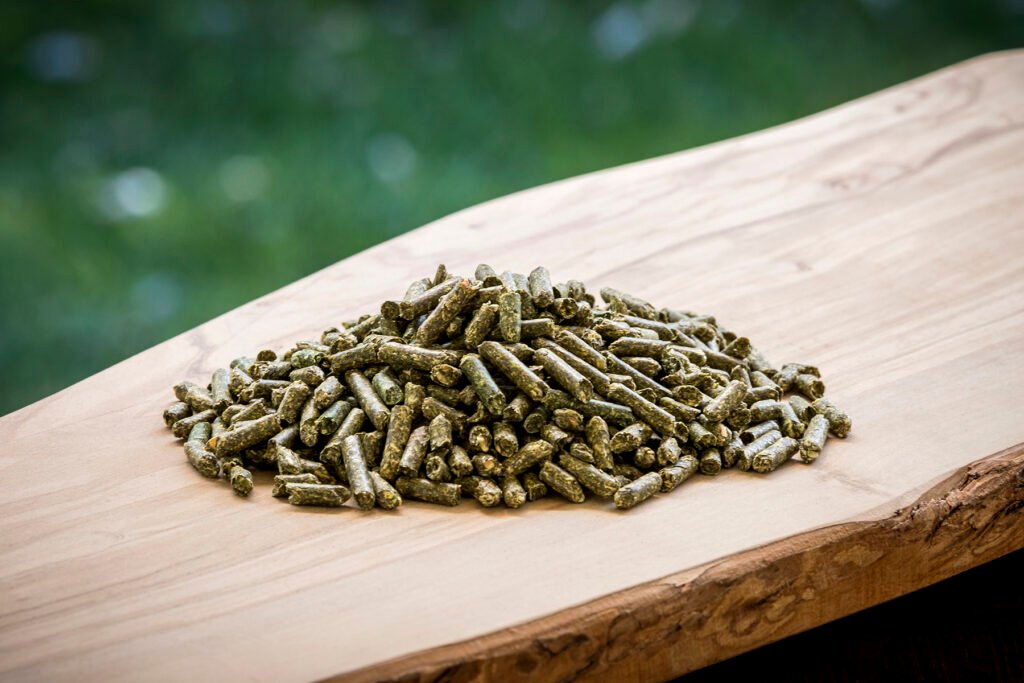
Project Cases and Solutions
Alfalfa pellet production lines, spanning capacities from 2 to 100 tons per hour, are intricate systems that encounter various technical hurdles. In this article, we delve into several actual project cases, detailing the specific technical problems encountered and the precise methods employed to overcome them, with a focus on ring mold technology.
Project Case 1: Moisture Control Optimization for 50 Tons per Hour Line
In a project targeting a production capacity of 50 tons per hour, moisture control emerged as a critical technical challenge. Inconsistent moisture levels in the alfalfa feedstock led to variations in pellet density and quality, affecting overall production efficiency.
To address this issue, our technical team implemented advanced moisture sensing and control systems throughout the production line. By integrating real-time moisture monitoring devices and automated control mechanisms, we achieved precise regulation of moisture content, ensuring uniform pellet formation and optimizing production throughput.
Project Case 2: Minimizing Dust Emissions in 20 Tons per Hour Setup
Dust emissions during the pelletizing process presented a significant technical challenge in a project with a production capacity of 20 tons per hour. High levels of airborne dust not only posed environmental and safety concerns but also affected equipment performance and operator health.
To mitigate dust emissions, our engineering team implemented a multi-faceted approach, including the installation of dust collection and filtration systems, the use of anti-dust additives in the feedstock, and the optimization of pellet mill parameters.
By effectively capturing and controlling dust particles, we ensured compliance with regulatory standards and created a safer and more sustainable production environment.
Project Case 3: Maximizing Energy Efficiency in 100 Tons per Hour Line
For a high-capacity alfalfa pellet production line targeting 100 tons per hour, maximizing energy efficiency was a paramount concern. The energy-intensive nature of pelletizing processes posed challenges in achieving optimal energy utilization without compromising production output.
To address this, our technical team conducted a comprehensive energy audit of the production line, identifying areas of inefficiency and opportunities for improvement. By implementing advanced process control algorithms, heat recovery systems, and equipment upgrades, we optimized energy consumption while maintaining high production throughput, resulting in significant cost savings and environmental benefits.
Project Case 4: Ensuring Pellet Quality in 2 Tons per Hour Pilot Line
Even in smaller-scale pilot projects with a production capacity of 2 tons per hour, ensuring consistent pellet quality is essential for evaluating feed performance and market acceptance. Variations in pellet density and durability posed technical challenges that required meticulous attention to detail.
To address this, our technical team conducted rigorous testing and optimization of ring mold parameters, including die specifications, compression ratios, and cooling techniques.
Additionally, stringent quality control measures were implemented throughout the production process to monitor pellet quality and ensure compliance with industry standards. By prioritizing quality assurance, we established a solid foundation for future scale-up and commercialization efforts.
In conclusion, technical challenges in alfalfa pellet production lines spanning capacities from 2 to 100 tons per hour can be effectively addressed through innovative solutions tailored to the specific requirements of each project. By leveraging ring mold technology and drawing upon our technical expertise, we ensure seamless operation, consistent pellet quality, and optimal production efficiency, thereby maximizing the success of alfalfa pellet production endeavors.
Supplier Selection and RICHI Machinery: A Winning Combination
Choosing the right supplier for alfalfa pellet making machines is paramount to the success of pellet production endeavors. Characteristics of an ideal supplier include expertise in pellet production technology, a track record of delivering customized solutions, reliable after-sales support, and a commitment to quality and innovation.
RICHI Machinery exemplifies these qualities, offering a comprehensive range of pellet production line solutions tailored to the specific requirements of customers worldwide. With its turnkey project capabilities, RICHI Machinery ensures end-to-end support, from project design and equipment selection to installation, commissioning, and training, thereby enabling customers to optimize their pellet production operations efficiently.
Summary and Necessity of Choosing Alfalfa Pellet Making Machines
In summary, alfalfa pellet making machines represent a crucial asset for modern agriculture and animal feed industries, offering a sustainable and efficient solution for alfalfa processing and utilization.
The selection of high-quality pellet making machines and reliable suppliers, such as RICHI Machinery, is essential for achieving optimal results, maximizing profitability, and ensuring long-term success in alfalfa pellet production endeavors.
Frequently Asked Questions
What factors should be considered when selecting an alfalfa pellet making machine?
Key factors to consider include production capacity, pellet quality, energy efficiency, equipment durability, after-sales support, and supplier reputation.
Can alfalfa pellet making machines process other types of feedstock besides alfalfa?
Yes, alfalfa pellet making machines can be adapted to process various types of biomass and feed ingredients, offering flexibility in feed formulation and production.
How can RICHI Machinery assist in overcoming challenges in alfalfa pellet production projects?
RICHI Machinery provides comprehensive turnkey project solutions, including project design, equipment selection, installation, commissioning, and after-sales support, ensuring seamless project execution and optimal performance.
What are the benefits of using alfalfa pellets in animal feed?
Alfalfa pellets offer numerous benefits, including high protein content, digestibility, palatability, and nutrient density, contributing to improved animal health, growth, and productivity.
In conclusion, alfalfa pellet making machines offer a transformative solution for alfalfa processing and utilization, with RICHI Machinery standing out as a reliable partner in realizing the full potential of alfalfa pellet production endeavors.